Как оптимизировать процессы
Процессы постоянной оптимизации — это важнейший аспект lean-производства. Совершенствование продукта и процессов — ведущие принципы бережливого производства.
Процесс оптимизации в данной концепции — это процесс постоянного уменьшения издержек и поиска таких возможностей. Оптимизация процесса при этом должна идти не сверху, а снизу. Именно сотрудники лучше всего видят, от каких операций возможно безболезненно отказаться.
Для этого наш отдел бережливого производства постоянно собирает предложения от сотрудников. Этот процесс возможен также благодаря инструментам, о которых мы поговорим ниже.
Что такое Lean: бережливое производство для чайников
Прежде всего, сделаем краткий ликбез по теме бережливого производства (Lean). Эта концепция управления предприятием предполагает непрерывное устранение всех видов потерь с целью максимальной оптимизации бизнеса для наилучшего удовлетворения потребителя. Она основана на производственной системе японской компании Toyota, благодаря которой автоконцерн вышел из послевоенного кризиса и стал успешной организацией в мировом масштабе. Идеи бережливого производства отражены во множестве современных методов управления качеством, наиболее популярными из которых считаются следующие :
- вытягивание, когда объёмы продукции и сроки её изготовления на каждом производственном этапе определяются исключительно потребностями заказчика, а не заранее разработанным и спущенным сверху планом;
- точно вовремя (Just in Time), когда движение материальных потоков организовано так, что все материалы и компоненты, необходимые для реализации готовой продукции, поступают в необходимом количестве, в нужное место и точно к назначенному сроку, не занимая место на складах;
- канбан – визуализация состояния рабочих задач для повышения прозрачности процессов и равномерного распределения нагрузки между их участниками;
- быстрая переналадкаоборудования (SMED, Single-Minute Exchange of Dies), когда его ремонт и переоснастка выполняются с высокой скоростью по заранее определенным схемам;
- автономизация оборудования, когда оно способно самостоятельно обнаружить проблемы, диагностировать и устранять собственные неисправности, сразу останавливая производственный процесс и сигнализируя об этом при выявлении дефектов в качестве продукции или задержек в работе;
- система 5S для организации и рационализации рабочего места или пространства, суть которой заключается в сортировке, соблюдении порядка, содержании в чистоте, стандартизации и совершенствовании установленных правил, процедур и технологических операций;
- защита от дурака, когда конструктивные или другие технологические особенности реализации решения не позволяют использовать его неверно.
Иногда к методам бережливого производства еще относят концепцию 6 сигм, основанную на статистических методах управления качеством для измерения отклонений реальной продукции от заданного эталона и сокращения дефектов. Однако, при общих целях повышения эффективности рабочих процессов и итоговых результатов, подход 6 сигм отличается от принципов Lean, а потому не входит в понятие бережливого производства. Тем не менее, на практике возможно совместное применение этих концепций для комплексного улучшения производственной деятельности и повышения удовлетворенности клиентов . Не случайно профессиональный стандарт бизнес-аналитика, руководство BABOK, включило методы Lean и 6 сигма в наиболее часто используемые техники процессного анализа.
«Бережливые» идеи в России
В России внедрение бережливого производства поддерживается на государственном уровне. Сегодня активное использование технологии бережливого производства особенно актуально на фоне борьбы с коронавирусом и его последствиями для экономики. Еще в 2018 году был утвержден Национальный проект «Производительность труда и поддержка занятости», призванный создать условия для ежегодного прироста производительности труда в стране на 5% к 2024 году.
Приказом Минпромторга России утверждены «Рекомендации по применению принципов бережливого производства в различных отраслях промышленности». Документ устанавливает единые подходы к применению принципов бережливого производства в разных типах организаций, в том числе в таких сложных интегрированных структурах, как холдинги, концерны и корпорации. В числе первых российских компаний, которые внедрили бережливое производство, были РЖД, «Почта России», Сбербанк, а также Госкорпорация Ростех и ее предприятия. Корпорация уже запустила систему бережливого производства на КАМАЗе, в холдингах «Швабе», «Вертолеты России», «Технодинамика», концернах КРЭТ и «Калашников», Объединенной двигателестроительной корпорации (ОДК) и др.
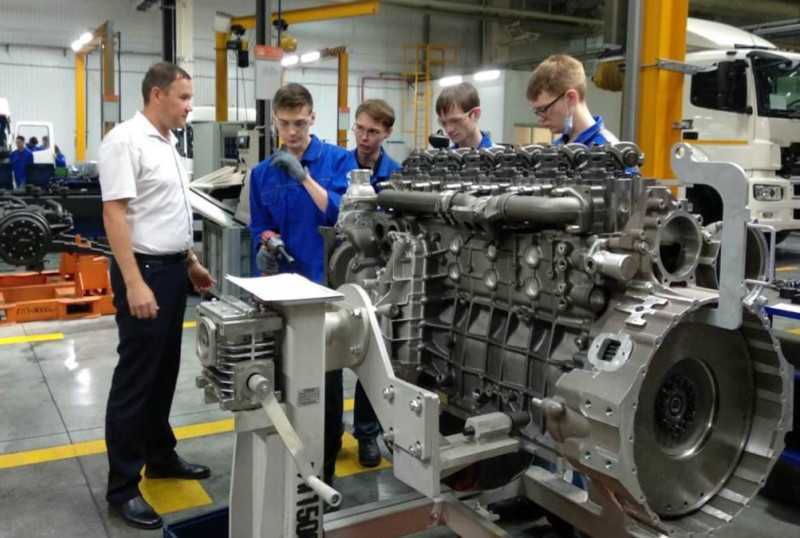
Фото: КАМАЗ
Одним из самых первых примеров успешного внедрения Lean-технологий стал КАМАЗ. Компания запустила программу бережливого производства в 2006 году и уже добилась заметных успехов. Производительность труда повысилась в несколько раза, темп конвейера снизился более, чем вдвое. Сегодня количество кайдзен-предложений, подаваемых ежегодно на предприятии, исчисляется не тысячами, а десятками и сотнями тысяч. Таким образом каждый рабочий стремится на своем рабочем месте изменить что-то к лучшему. Ну, и самое главное доказательство эффективности системы – новые современные автомобили. Неудивительно, что команда ПАО «КАМАЗ» заняла первое место в чемпионате RostecSkills-2021 в компетенции «Бережливое производство».
Другой пример развития бережливого производства в Корпорации – «Калашников» открыл лабораторию Lean-процессов, которая позволяет ускорить разработку и внедрение рационализаторских предложений. Лаборатория вмещает восемь модульных зон – здесь полностью имитируется полноценное производство. Имеются также классы теоретического обучения, где рассказывают о картирования офисных процессов, «кайдзен», 5С-процессах и др.
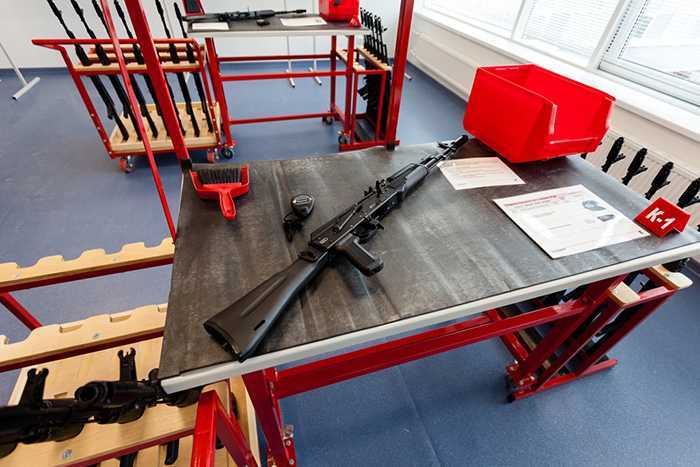
Фото: Калашников
Внедрение методов бережливого производства позволило «Калашникову» значительно увеличить производительность труда, повысить скорость обработки серийных деталей для стрелкового оружия. По итогам прошлого года Концерн вошел в тройку призеров всероссийского конкурса по бережливому производству имени А.К. Гастева. Это самый масштабный в России и СНГ проект по бережливому производству, рассказывающий об опыте организаций, компаний и корпораций.
Объединенная двигателестроительная корпорация Ростеха приступила к освоению бережливого производства в 2010 году – за это время удалось выстроить целостную систему, обеспечивающую непрерывность преобразований и ежегодный экономический эффект. Например, по итогам 2020 года, сотрудниками ОДК подано несколько десятков тысяч предложений, а количество реализованных проектов по развитию производственной системы превысило запланированный уровень почти в два раза.
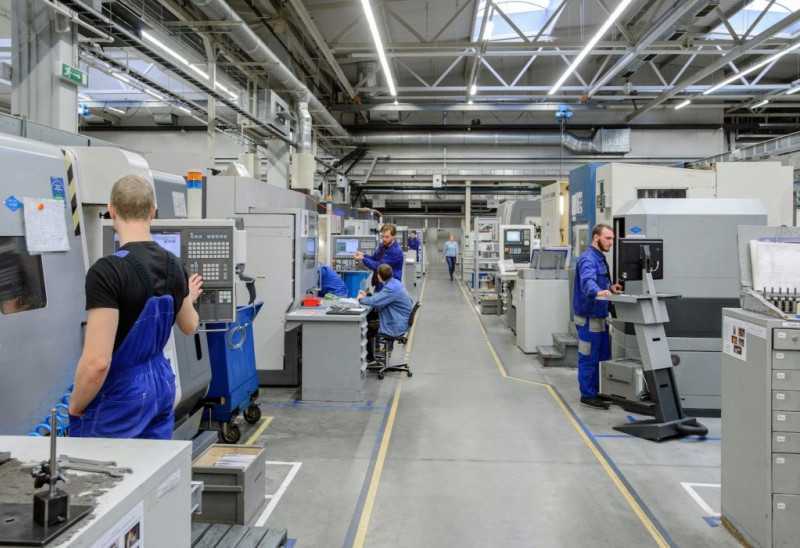
Фото: ОДК
Важную роль в вовлечении сотрудников ОДК стала такая практика как мастерские по преобразованию производственной системы. Мероприятия подобного формата уникальны для Ростеха. Всего за 3-4 дня участники мастерской могут получить опыт и навыки по решению реальных проблем предприятия с применением инструментов бережливого производства. В этом им помогают выпускники практики и приглашенные эксперты. Такие мастерские проходят в ОДК ежегодно с 2012 года, в них приняли участие 1022 работника и инициировано более 100 проектов.
Сейчас в ОДК реализуется программа «Трансформация индустриальной модели», которая включает в себя создание центров специализации и уход от модели производства предприятий «полного цикла». Программа направлена на сокращение затрат, повышение эффективности производства и усиление концентрации инвестиций в техперевооружение – для этого все центры специализации изначально создаются на принципах бережливого производства.
Проект внедрения бережливого производства
Общая суть внедрения концепции бережливого производства заключается в следующем. Формируется проект по запуску бережливого производства на предприятии. Для участия в таком проекте формируется команда высококвалифицированных специалистов, имеющих опыт работы в Lean. После начала работ по проекту анализируется текущее состояние производства, выявляются не добавляющие ценность процессы и формируется видение будущего бережливого предприятия. После основных этапов подготовки проекта по переходу на бережливое производство, постепенно выполняются мероприятия по устранению потерь, созданию потока, формированию необходимых знаний у сотрудников, анализ и оценка полученных результатов, а также поддержание этих результатов и стандартизация полученных знаний.
Этапы проекта
Независимо от масштабов предприятия внедрение бережливого производства рекомендуется начинать с конкретного процесса на предприятии, постепенно двигаясь вверх к масштабам расширенного предприятия. Этапы такого внедрения стратегий и используемых инструментов представлены в таблице.
Таблица из книги “Практика ДАО Тойота”
Начальные этапы процесса, например, разработка продукции оказывают на производство эффект мультипликатора, который в значительной мере превосходит инвестиции в разработку. Так почему же рекомендуется начать внедрение бережливого производства именно с предложенных областей? Опыт Тойота говорит о том, что если преждевременно начать внедрение бережливого производства на уровне предприятия или расширенного предприятия, то вреда будет больше, чем пользы, по ряду следующих причин:
- Бережливое производство проще понять на процессах материального характера. Проще всего добиться существенных измеримых результатов на производственных процессах, которые осуществляются каждый день и содержат в себе большинство потерь. Для организаций оказания услуг — внедрение бережливого производства необходимо начинать в самых часто повторяющихся операциях.
- Опасность превысить возможности имеющихся ресурсов. Группа сотрудников, занимающихся внедрением бережливого производства, должна начать работу по созданию добавленной ценности на небольшом участке для того, чтобы лучше усвоить бережливую тактику.
- При оказании услуг бережливые процессы должны поддерживать важнейшие операции по добавлению ценности. Любой проект по внедрению бережливого производства должен начинаться с определения цели бизнеса: кто ваш потребитель? Каковы его нужды? Если потребителем процесса оказания услуг является процесс физического видоизменения материала, сначала нужно пойти и посмотреть, каков будет этот процесс после трансформации, чтобы понять, как обеспечить его поддержку.
- Опасность превратить бережливое производство в модную тенденцию. Нередко внедрение бережливого производства проводится только на важнейших процессах, в то время как вспомогательные процессы остаются без внимания. Бережливое производство не должно превращаться в программу одного месяца, важнее сделать правильно, чем быстро.
- Попытка заставить поставщиков освоить бережливое производство, прежде чем это сделали вы. Бережливая цепочка поставок предполагает наличие комплекса иерархически взаимосвязанных компонентов, и если вы возьметесь за развитие и обучение поставщиков, не создав доверия и взаимопонимания, поставщики будут рассматривать такое обучение как компенсацию за давление на них по поводу цены.
Технология внедрения методов бережливого производства
Алгоритм реализации может быть
представлен в восемь этапов:
- найти агента перемен (вам нужен лидер, который может взять на себя ответственность).
- получить необходимые знания о системе бережливости (из надежного источника).
- найти или создать кризис (хорошим мотивом для введения lean является кризис в организации).
- не увлекайтесь стратегическими вопросами (вы можете начать с устранения потерь там, где это возможно).
- создавать карты потоков ценности (сначала текущее состояние, а затем будущее состояние, после бережливого внедрения).
- как можно скорее начать работу по ключевым областям (информация о результатах должна быть доступна сотрудникам организации).
- стремиться к достижению немедленных результатов.
- осуществлять непрерывное совершенствование в соответствии с системой Кайдзен (переход от процессов с добавленной стоимостью в магазинах к административным процессам).
Для создания бережливой культуры
необходимо изменить корпоративную культуру в организации. Примером тому
является служебная записка сотрудника ОАО «КУМЗ»:
- Мы можем делать все, что захотим.
- Мы знаем рынки, которые мы обслуживаем.
- Мы гордимся нашими продуктами и соответственно ценим их.
- Мы стараемся меняться каждый день и тем самым делать качественный скачок.
- Мы сильны, подвижны, предприимчивы.
- Мы привержены бережливым решениям.
- Мы вознаграждаемся результатами, а не позициями.
- Мы следуем правилу: «Не приходите с проблемой, приходите с решением».
- Мы говорим: «Плохое решение лучше, чем вообще никакого решения».
- И последнее — «Босс занят, так что будь боссом».
Трудности при внедрении системы 5S
В то же время, при внедрении системы 5S, российские предприятия сталкиваются с двумя основными проблемами: сопротивление сотрудников нововведениям и недостаточная вовлеченность руководства во внедрение системы на предприятие.
Внедрение любых нововведений в рабочий процесс всегда является стрессом для сотрудников и вызывает осознанное или неосознанное сопротивление, поэтому внедрение системы 5S часто сталкивается с недовольством и страхами сотрудников. Несправедливое распределение нагрузки, переработки, необходимость перестраивать привычное пространство и отказываться от привычных вещей — все эти факторы негативно воспринимаются работниками.
Очевидно также, что российский, японский, американский менталитеты различаются и сотрудники российских предприятий не видят смысла работать на «цели компании» и увеличивать прибыль, поскольку воспринимают коллективные цели только как обогащение руководства компании.
Многих сотрудников пугают возможные сокращения, рост ответственности, необходимость тратить время на обучение, тренинги, совещания (особенно при сдельной оплате труда). Сопротивление сотрудников может свести на нет все усилия компании по внедрению бережливого производства: формальное выполнение требований менеджмента, сознательное саботирование инструкций, снижение мотивации и снижение качества работы, увольнение квалифицированных кадров — риски, с которыми сталкивается практически каждая российская компания при попытке внедрить систему 5S и другие принципы бережливого производства.
Еще более важным и рискованным с точки зрения внедрения системы 5S является отношение руководства предприятия к данной затее. Многие предприятия отказываются от внедрения системы, считая ее просто модной, «раскрученной» западной идеей, не применимой в российских условиях. Отсутствие адаптации этой системы к условиям конкретного предприятия и к традициям, нормам конкретного коллектива, особенно если для внедрения системы привлекаются внешние консультанты и контролеры — тоже сводят усилия на нет. Использование иностранных, особенно японских, терминов усиливает скептицизм сотрудников, снижает доверие к «новомодному феншую» и тормозит появление тех позитивных изменений в организации, для которых создавалась система 5S.
Основные принципы, цели и задачи бережливого производства
Бережливое производство нацелено на
устранение потерь во всех областях производства, включая отношения с
заказчиками, проектирование продукции, цепочку поставок и управление
производством. Целью такого производства является достижение минимальных
трудозатрат, минимального времени на создание новой
продукции, гарантированной доставки продукции заказчику, высокого качества при
минимальных затратах.
Концепция бережливого производства
предполагает развитие миссии, формирование целей и задач. Они разные для каждой
компании. Из этого вытекают задачи:
- Формировать принципы выявления узких мест;
- Планирование и управление пилотными проектами в рамках всей производственной системы компании;
- Разработка стандарта компании по организации и функционированию бережливого производства;
- Формирование оценки показателей эффективности пилотных проектов и методов стимулирования их участников;
- Организация тиражирования передового опыта отделов для общего использования в рамках группы (максимальное качество при минимальных затратах).
Это достигается путем применения
следующих принципов:
- тяговое производство (продукция «тянется» заказчиком, а не навязывается изготовителем, последующие операции сигнализируют о необходимости предыдущих операций).
- выдающееся качество (в порядке поступления, в порядке очередности, система с нулевыми дефектами, поиск и решение проблем у источника)
- минимизация навоза путем исключения всех видов деятельности, не приносящих пользы клиенту, максимизация использования всех ресурсов (капитала, людей, земли).
- постоянное совершенствование (снижение затрат, повышение качества используемой продукции и информации, повышение производительности).
- гибкость.
- выстраивать долгосрочные отношения с клиентом, разделяя риски, затраты и информацию.
Тяговое производство — это метод
управления производством, при котором последующие операции сообщают о своих
требованиях к предыдущим операциям.
Существует три вида тягового
производства:
- Система выдвижения в супермаркетах (система возврата/возврата) — система выдвижения типа А;
- Последовательная железнодорожная система — система поездов типа B;
- смешанная железнодорожная система — система поездов типа С.
Наиболее популярной является система
розыгрыша в супермаркетах. На каждом этапе производства находится склад —
супермаркет, в котором хранится определенное количество продукции,
произведенной на этом этапе. На каждом этапе производится столько же продукции,
сколько взято из супермаркета. Когда продукты забираются из супермаркета
последующим процессом — потребитель, как правило, посылает информацию об
изъятии с помощью специальной карточки (kanban) или иным способом вплоть до
предыдущего процесса.
Каждый процесс отвечает за
пополнение своего супермаркета, поэтому управление операциями и поиск объектов
постоянного улучшения (кайдзен) не представляет особой сложности. В то же время
его применение затруднено при наличии большого количества видов производимой продукции
Последовательная система изъятия
пригодна в тех случаях, когда в супермаркете производится широкий ассортимент
продукции в рамках одного процесса, т.е. когда хранение запасов каждого вида
продукции в супермаркете затруднено или практически невозможно. Продукты, по сути, изготавливаются на заказ, при этом общие
запасы в системе сведены к минимуму. Последовательная система требует
поддержания короткого и предсказуемого срока выполнения, необходимо хорошо
знать структуру поступающих заказов клиента. Эксплуатация
такой системы требует очень сильного управления.
Смешанная железнодорожная система
является комбинацией двух вышеуказанных систем. Это уместно, когда действует
правило 80/20, т.е. когда на небольшую долю видов продукции (прибл. 20%)
приходится наибольшая доля суточной выработки (прибл. 80%).
Все виды продукции делятся на
сервисные группы: большие партии, средние партии, малые партии и редкие заказы.
Для группы «редких ордеров» имеет смысл использовать систему
последовательного рисования. Для других групп подходит система розыгрыша в
супермаркетах. При смешанной системе вытяжки будет
сложнее управлять улучшениями и выявлять отклонения.
Бережливое производство основные принципы (Lean production, Lean manufacturing).
В настоящий момент существует 5 принципов:
Чтобы лучше понять первый принцип определения потребительской ценности, важно понять, что такое ценность. Ценность — это то, за что клиент готов платить
Это имеет первостепенное значение для выявления фактических или скрытых потребностей клиента. Иногда клиенты могут не знать, чего они хотят, или не могут сформулировать это. Это особенно распространено, когда речь идет о новых продуктах или технологиях. Существует множество методов, таких как интервью, опросы, демографическая информация и веб-аналитика, которые могут помочь вам расшифровать и выяснить, что клиенты считают ценным. Используя эти качественные и количественные методы, вы можете узнать, что клиенты хотят, как они хотят, чтобы продукт или услуга были доставлены, и за цену, которую они себе представляют.
На этом этапе цель состоит в том, чтобы, используя ценность клиента в качестве ориентира идентифицировать все действия, которые способствуют созданию ценности. Действия, которые не увеличивают ценность для конечного потребителя, считаются потерями. Потери можно разбить на две категории: неценные добавленные, но необходимые и неценные, и ненужные. Последние являются чистыми потерями и должны быть устранены, в то время как первые должны быть максимально сокращены. Сокращая и устраняя ненужные процессы или этапы, вы можете гарантировать, что клиенты получают именно то, что им нужно, и в то же время снижать стоимость производства этого продукта или услуги. Для оптимизации работы и выявления потерь необходимо детально описать все действия от момента получения заказа, до поставки продукции потребителю.
Виды потерь в основном рассматривают по 8 видам:
- Перепроизводство
- Излишние запасы
- Дефекты
- Действия не создающие ценности
- Ожидание
- Излишние передвижения
- Транспортировка
Неиспользованный потенциал сотрудников
Необходимо обеспечение бесперебойной работы всех этапов без прерываний и задержек. Некоторые стратегии для обеспечения бесперебойного выполнения операций по добавлению стоимости включают в себя: разбивку этапов, перенастройку этапов производства, выравнивание рабочей нагрузки, создание межфункциональных отделов и обучение сотрудников навыкам работы с разными навыками и адаптивность. Это может потребовать перепроектирования процессов или применения новых технологий. Все действия должны добавлять ценность продукту.
Запасы считаются одними из самых больших потерь в любой производственной системе. Целью системы, основанной на «вытягивании», является ограничение запасов и незавершенного производства (WIP), обеспечивая при этом необходимые материалы и информацию для бесперебойной работы. Другими словами, система, основанная на «вытягивании», позволяет осуществлять доставку и производство точно в срок, когда продукты создаются в то время, когда они необходимы, и только в необходимых количествах. «Вытягивание» выполняется с учетом потребностей конечных клиентов. Следуя потоку создания ценности и работая в обратном направлении через производственную систему, вы можете быть уверены, что произведенная продукция сможет удовлетворить потребности клиентов.
Потери предотвращаются посредством выполнения первых четырех этапов: 1) определения Ценности, 2) Отображения потока создания ценности, 3) Построение непрерывного потока и 4) «Вытягивание» потока. Тем не менее, пятый шаг к достижению совершенства является наиболее важным среди них всех. Это формирует мышление Бережливого производства (Lean thinking) и постоянное совершенствование процесса, частью организационной культуры. Каждый сотрудник должен стремиться к совершенству, предоставляя продукцию в соответствии с потребностями клиента. Компания должна стать обучающейся организацией и всегда находить способы становиться немного лучше каждый день. Разумно и планомерно используя принципы Бережливого производства, только так, реально достичь высоких результатов!
Принципы Бережливого производства – основные инструменты.
Бережливое производство (Lean) не может быть разовым мероприятием, данная методология построена на непрерывном улучшении. Для этого используется очень много инструментов. Вот некоторые из них:
- Метод 5S
- Устранение Потерь (Муда).
- Картирование потока
- Канбан
- Защита от Ошибок
- Быстрая переналадка (Single-Minute Exchange of Dies (SMED).
- Андон
Наблюдение со стороны
Грандиозный успех Тойоты не давал покоя американским компаниям, и они принялись его изучать, профинансировав исследовательский проект по анализу мирового автомобильного рынка, который возглавили Джеймс Вумек и Дэниел Джонс.
в результате данных исследований появился термин Lean Production.
Lean с английского переводится как тощий или худой. т.е. Lean Production означает такой тип производства, в котором нет ничего лишнего, где система работает с минимальным количеством запасов и высоком уровне качества в противоположность традиционному подходу к производству, накапливающему запасы в том числе содержащие дефектные детали.
Далее концепция бережливого производства трансформировалась в идею бережливого мышления, предлагающего применение принципов бережливости к любому производству или сфере услуг.
В России существовала система научной организации труда, идеи которой перекликаются с основами TPS. Одним из основоположником в СССР в данном направлении был Алексей Гастев. В своей книге 1922 года «Как надо работать» Гастев описывал те правила, которых должен придерживаться рабочий при организации производственного процесса (соблюдение порядка на рабочем месте, равномерная загрузка и т.д.). Эти правила перекликаются с TPS.
В настоящее время, бережливое производство получает все большее распространение в России. С каждым годом растет количество компаний, внедряющих эти подходы.
Вот только некоторые компании, стремящиеся стать бережливыми
Применения в отраслях
Бережливое производство на примерах внедрения в различных отраслях по всему миру демонстрирует универсальность. Сначала концепция применялась только в отраслях с дискретным производством, затем она была адаптирована к процессному производству, а со временем те же идеи начали применяться в сфере услуг, коммунальных хозяйствах, вооружённых силах, системе образования, секторе государственного управления и др.
- Здравоохранение. Здесь концепция применяется к сокращению временных затрат медицинского персонала, за исключением времени, отводимого на оказание непосредственной помощи пациентам. Минздрав России с помощью консультантов из Росатома с 2016 года проводит эксперимент по внедрению основных принципов бережливого здравоохранения в поликлиниках.
- Логистика. Широко применяется метод вытягивающего производства – создание цепи, в которую входят целый ряд поставщиков, вовлечённых в поток создания ценности. Фактически производится частичное регулярное пополнение запасов малыми партиями. Экономический эффект определяется по показателю совокупной логистической стоимости – TLC (total logistics cost).
- Почта. Датское почтовое ведомство, следуя идеям Lean, произвело масштабную стандартизацию услуг, что ускорило почтовые пересылки и идентификацию адресатов. Для оптимизации был применён метод картирования потока создания ценностей, что повлекло и внедрение системы мотивации служащих.
Известны также примеры внедрения Lean в строительной отрасли с повышением эффективности всех этапов деятельности, в сфере разработки программного обеспечения, в муниципальном управлении в виде разработки концепций «бережливого правительства» и «бережливого города».
Эффективность внедрения концепции в цифрах
Применение принципов Lean на предприятиях старой формации демонстрирует эффективность, которая увеличивает не на несколько процентов, а в несколько раз:
- В 3-10 раз увеличивается производительность.
- В 5-20 – сокращаются вынужденные простои.
- В 10-100 – укорачивается цикл изготовления.
- На половину и более уменьшаются складские запасы.
- В 50 раз уменьшается количество дефектов.
Цифры эти могут варьироваться в зависимости от отрасли и полноты применения всего набора инструментов. Из известных примеров:
- В электронной промышленности число этапов процесса производства сократилось с 31 до 9, что сократило цикл с 9 до 1 рабочего дня.
- В авиапроме срок выполнения заказа уменьшился с 1 года 4 месяцев до 4 месяцев.
- Автопром показал рост качества на 40%.
- В цветной металлургии производительность выросла на 35%.
Для наглядности абсолютной экономии можно привести следующие статистические показатели. На сборке автомобильных узлов при внедрении концепции Lean высвободилось порядка 20% производственных площадей, что повлекло за собой прекращение работ по проектированию и строительству нового цеха, в результате чего за неделю была сэкономлена сумма в 2,5 млн. долларов.